How do you prove your department's value? Discover the key purchasing performance metrics that showcase your team's ROI, efficiency, and strategic impact.
Purchase performance criteria or metrics values that make all aspects of purchasing goods and services measurable. Performance indicators enable the purchasing department to control and optimize the quantity, quality, costs, timing and supply of the purchases.
Compliance Rate
Can your suppliers meet your requirements?
Compliance is an important component in providing guidance and insight to all processes and helps you to build better relationships with your suppliers saving costs.
Assists in assessing supplier’s compliance with business requirements. The entire procurement function is built upon the basic agreement between supplier and company. This agreement includes lead time, special offer discounts, maximum time to respond in case of latency or issue, mode of payment, etc. and so on. A decrease in the compliance rate KPI will lead to an increase in indirect procurement or voluntary expenditures.
Provide insights into supplier relationships and help save costs through negotiations with suppliers. The metrics contributing to this KPI are the difference between the ratio of the disputed invoices to the total invoices for that supplier and the price paid and the price quoted. Working with certified suppliers improves compliance metrics significantly because they have a better understanding of processes and work methodologies.
Performance Indicators
For the average company not operating worldwide with millions of suppliers or users, it is a good goal to achieve a 50% compliance overall.
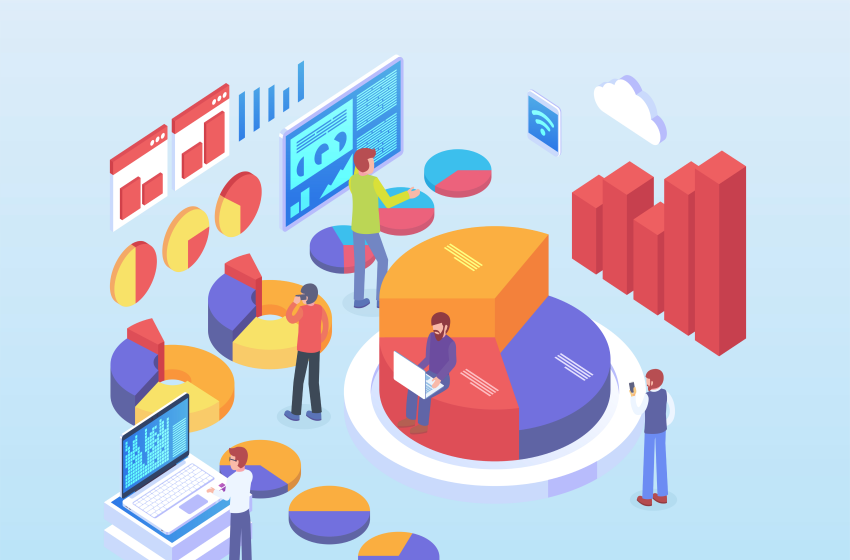

Purchase Order Cycle Time
Know who to place your immediate orders
The purchase order cycle time is the period from when a purchase requisition is submitted to a supplier or contractor. The entire purchase order cycle is in the scope of this KPI.
Order creation, confirmation, delivery, invoice creation and payment are steps in the purchase order cycle. The PO (Purchase Order) cycle time can vary from hours to days. Suppliers responding to urgent orders can be determined from the value of this metric. Depending on the value of the cycle time, suppliers can be divided into several categories.
For example, suppliers with a PO cycle time of 4 days or less may be classified as short, a cycle time of 5 to 8 days is medium, a cycle time greater than 8 days is long.
Urgent order may be placed with a vendor with a short PO cycle time. Overall cost and productivity of the procurement function and staff productivity can be improved by reducing the PO cycle time.
A purchase order is a process between a buyer and a vendor that is used to purchase material. The price, terms, conditions and additional obligations of the product or service must be specifically defined. The order form to be prepared must contain all the details and include date and signature locations.
The form for purchase orders should generally be delivered by fax, email or other electronic means. In some cases, delivery mode must be specified on the invoice. It is also very important to get your urgent orders from which supplier.
Performance Indicators
Reducing your cycle time can increase the return on other key activities and increase staff efficiency and the total cost of procurement functionality.
Improve your purchasing performance with SmartProcure
Contact us now to have unlimited influence and power
If You Want Call First
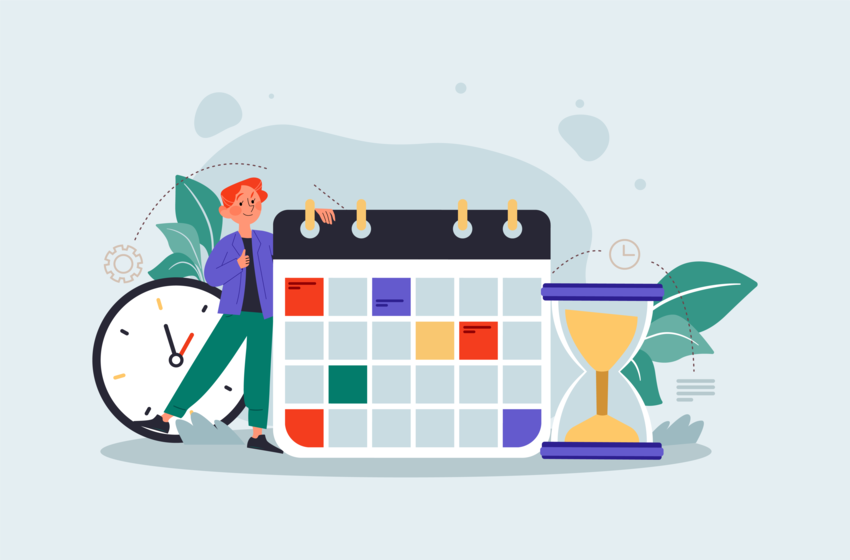


Lead Time
Measure the total time to fulfill an order
The Lead Time Metric measures the time between starting a purchase action and placing the production model in the purchased procurement system as a result of that action. In other words, the delay between starting and executing a transaction.
Consists of production lead time and administrative lead time. For example, the delivery time between the placement of an order and the delivery of the printed circuit boards from a manufacturer might be 2 weeks to 3 months or sometimes more.
The delivery time is different from the purchase order cycle time because the cycle time ends with order confirmation and starts until the last delivery and test when the request is made. Determine the amount of target days that must fall below the deadline; if you observe a failure over time, precautions must be taken.
-
The purchase of the production model is the final result of starting the purchase of the goods/service.
-
The lead time is a measure of the delay between starting the process and completing it.
-
The delivery time for a vendor or supplier is the period between the receipt of a purchase order and the time the order is dispatched.
-
The delivery time should not be confused with the PO(Purchase Order) cycle time since both refer to different time zones.
-
The delivery period starts upon request and ends after final delivery and testing; The PO cycle time starts at the beginning of the request and ends when the order is approved.
-
Delivery time is the sum of the production lead time and administrative delivery time.
Performance Indicators
The idea is to reduce lead time as much as possible while maintaining a good quality level.
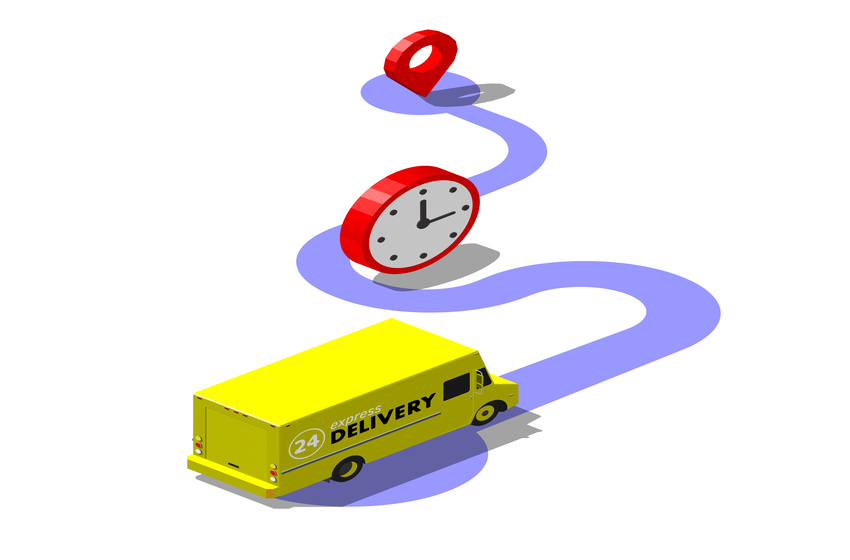
Emergency Purchase Ratio
Track emergency purchases
Urgent purchase rate is a purchase KPI, focusing on unplanned orders. These orders are usually done when there is a product shortage indicator and are measured over a period of time, expressed as a percentage between emergency purchases and total purchases.
Additional details about the emergencies that occur can also affect the quarterly project average. In essence, if this metric is lower, the organization has the opportunity to save costs, improve planning processes and reduce supply risks, among other important impacts.
These indicators will, as a result, show you how effective your planning is and whether you should adjust future strategies.
While it is normal for a business to have ad-hoc demands, the existence of a large number of unplanned purchases is poorly reflected in the procurement strategy. Urgent purchase rate is a KPI that sheds light on unplanned orders. Emergency purchases are usually made when there is a shortage of operations, products or services.
Emergency purchases are typically made at higher purchase rates, so the lower the emergency purchases, the better the productivity at work.
-
Having a low emergency purchase rate helps businesses
-
Save costs
-
Streamline supply plans
-
Ensuring continuity (availability) of goods
-
Minimize supply risks
This measure is a reflection of the effectiveness of the procurement strategy and a guide for planning future strategies. Efforts to keep emergency purchase rates low will help businesses avoid process bottlenecks and product shortages in the product portfolio.
Performance Indicators
The aim is to keep the ratio as low as possible to avoid bottlenecks and shortages in your product portfolio.
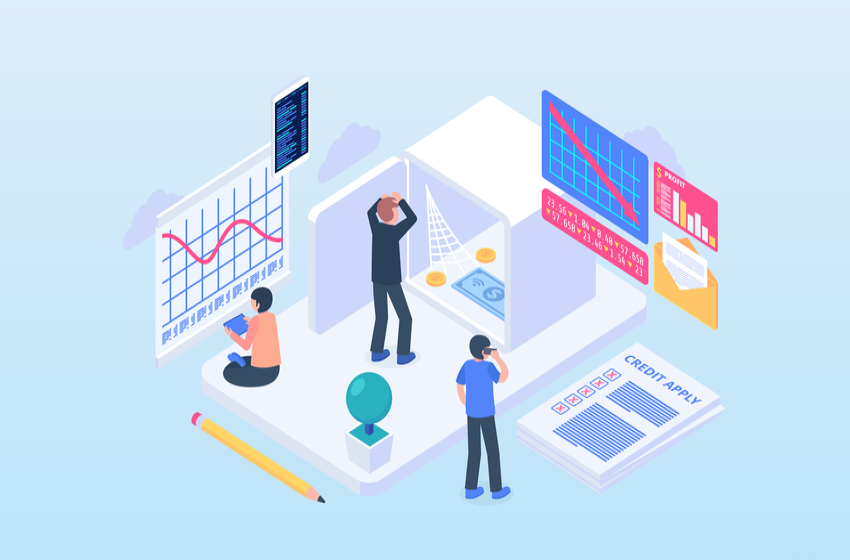
Cost of Purchase Order
Check your internal costs arising from purchases
Cost of the purchase order is one of the disputed procurement KPIs as definition and implementation vary. Theoretically, this metric represents the average costs of processing an order from the purchase process to the closing of the invoice.
So when you measure that metric, what you decide to consider is: what is the average cost for processing a purchase order based directly or indirectly on how long it takes by the related employee.
The KPI definition and implementation of purchase order cost may vary for each business. A broad definition of the cost of the purchase order is the average cost of purchasing an order until the purchase, creation, and invoice settlement. Practically speaking, the measurement of this KPI involves tracking several variables.
Each business comes with a different variable list that determines the cost of the purchase order. Some take into account direct and indirect costs, others may only consider direct costs and the time each order takes. It is important to understand the essence of tracking purchase order cost metrics; this is to increase the efficiency of the purchase life cycle and to keep errors and costs to a minimum. After understanding the purpose of measuring this KPI, businesses can decide which variables to consider in order to measure it.
Performance Indicators
The idea is to increase the efficiency of the purchase-pay cycle to avoid mistakes and reduce costs.
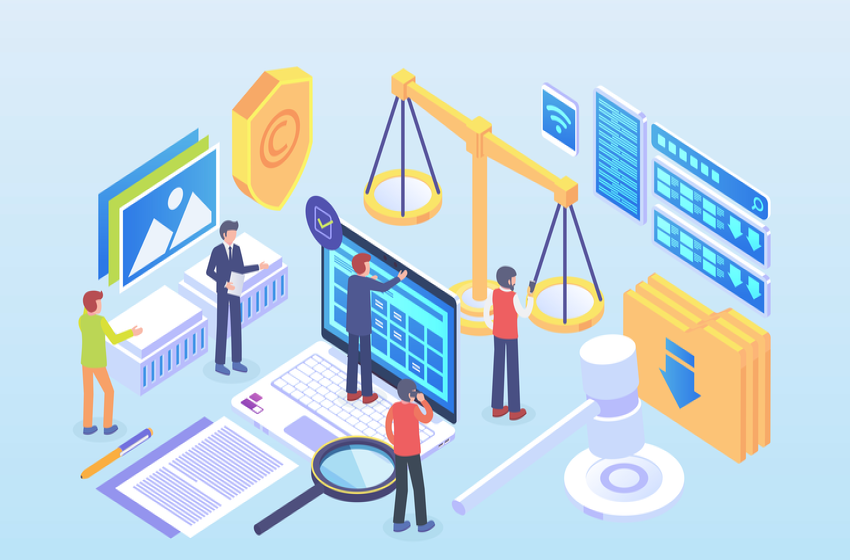